
Now some good things to know about AB PID blocks:ġ) Never put conditions on the branch that the PID is on - when the conditions turn TRUE (and enable the PID), the PID will think the system is wherever it last left off, and try to responnd to conditions that don't exist. Again it makes a difference (see below).Īs you said "Any help or information that will help me accomplish this task will be greatly appreciated."

Second question - do you have the analog module points (assume you are using a 1762-IF2OF2) configured for "Raw/Proportional" or "Scaled for PID". Verify that the 1200 uses the same words - this is shown on hte help screen for the PID block.įirst question - do you have one output (controlling both heating & cooling) or two (one each). You would consequently have your operator interface write the setpoint to N10:2. So, per the example in the manual, if your PID was assigned to control block N10:0 the setpoint would be N10:2. The way A-B soes it, each parameter is assigned to a specific word in hte control block. Clicking the Setup Screen on the PID block will take you to a set-up screen for the PID loop, with constants for setpoint and tuning accessible.

It shows the Process Variable (input) and Controlled Variable (outut) on the main block. You'll find the PID loop under the File/Misc tab in RSLogix 500. Any help or information that will help me accomplish this task will be greatly appreciated. I am using a pannel view writing to a Intenger file for the set point. A example of a PID loop used for a similar operation would be extremely helpful.
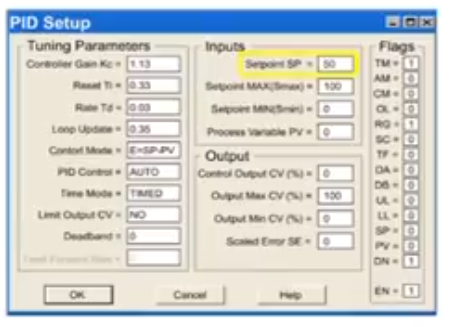
I am using the input to read temp (Using SCP) I want to control heat (reverse acting) / cool (direct acting) with the output. I have a Micrologix 1200 controler with 2 ch input/ 2 ch output analog module. Home Conferences *** LIVE PLC Q&A *** (Public) New Here? Please read this important info!!!

Your Personal PLC Tutor Site - Interactive Q & A Please DON'T use it for advertising, etc. Your Personal PLC Tutor Site - Interactive Q & A - "PID Loop"
